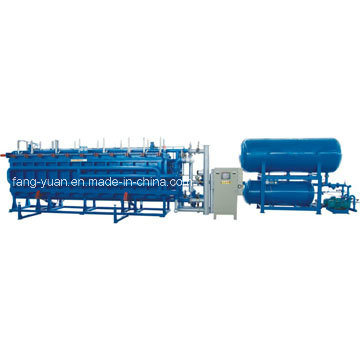
2.Technical Data of eps concrete sandwich wall panel machine
SPB200-800DZ eps foam concrete block machine (Typical) | ||||||
Item | Â | SPB200/DZ | SPB300/DZ | SPB400/DZ/ | SPB600/DZ | SPB800/DZ |
Mould Cavity Size |
 | 2040*1240 *1030(mm) |
3060*1240 *1030(mm) |
4080*1240 *1030(mm) |
6100*1240 *1030(mm) |
8120*1240 *1030(mm) |
Block Size |
 | 2000*1200 *1000(mm) |
3000*1200 *1000(mm) |
4000*1200 *1000(mm) |
6000*1200 *1000(mm) |
8000*1200 *1000(mm) |
Steam | Entry Consumption Pressure |
DN65 30-50kg/cycle 0.8MPa |
DN65 50-70kg/cycle 0.8MPa |
DN100 60-90kg/cycle 0.8MPa |
DN100 100-130kg/cycle 0.8MPa |
DN150 120-170kg/cycle 0.8MPa |
Compressed Air |
Entry Consumption Pressure |
DN40 1.5-2m3/cycle 0.6MPa |
DN40 1.8-2.2m3/cycle 0.6MPa |
DN40 2-2.5m3/cycle 0.6MPa |
DN40 2-3m3/cycle 0.6MPa |
DN40 2.5-3m3/cycle 0.6MPa |
Cooling Water |
Entry Consumption Pressure |
DN50 0.4 m3/ cycle 0.4-0.6MPa |
DN50 0.6 m3/ cycle 0.4-0.6MPa |
DN50 0.6 m3/ cycle 0.4-0.6MPa |
DN50 0.6-1 m3/ cycle 0.4-0.6MPa |
DN50 0.8-1.2m3/ cycle 0.4-0.6MPa |
Drainage | Vacuum drain Steam vent Condensate |
φ125mm φ00mm φ100mm |
φ125mm φ100mm φ100mm |
φ125mm φ200mm φ100mm |
φ125mm φ200mm φ100mm |
φ125mm φ200mm φ100mm |
Throughput | 15kg/m3 | 5min/cycle | 6min/cycle | 7min/cycle | 8min/cycle | 8min/cycle |
Connected Load |
 | 20.5-24.5KW | 20.5-24.5KW | 24.5-35.5KW | 24.5-35.5KW | 35.5-43.5KW |
Overall Dimension |
(L*W*H) | 5700*4000 *2850(mm) |
7200*4500 *3000(mm) |
11000*4500 *3300(mm) |
12600*3960 *2906(mm) |
15700*4600 *3400(mm) |
Weight | Â | 6000kg | 7200kg | 12000kg | 15000kg | 18500kg |
Room Height Required |
 | 6000mm | 6000mm | 6000mm | 6000mm | 6000mm |
Vote: We custom makeeps foam concrete block machine according to customer's requirement |
3.Features of eps concrete sandwich wall panel machine
1. EPS machinery With PLC and touch screen to control machine's whole, cycle, including opening mold, closing mold filling, steaming, stabilizing, Vacuum cooling and ejecting.
2. Made with excellent profile steel, through heating process to improve sturdiness, machine can bear high expansion force.
3. With efficient vacuum system for faster steaming and cooling, improve productivity and ensure even density of outer inner block.
4. Adopt advanced block making technology to produce high-density and low-density foam blocks, ensuring even density of outer block.
5. The surface of mold cavity is painted with Teflon, which easies block demoulding and beautifies surface of blocks. Utomatically weighing post-mold blocks.
6. Electronic weighing scale is equipped on block exit line for aEPS Block Molding MachineÂ
4.Application of eps concrete sandwich wall panel machine
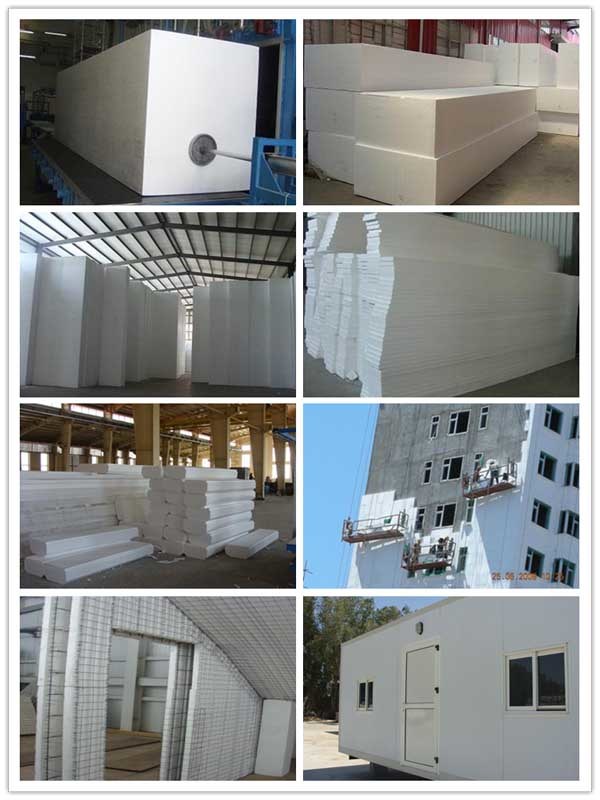
5.Packaging & Shipping
Packing:Â standard exporting packageÂ
Shipping port:Â shanghai/ningbo
6.WE can provided this service of eps Foam Blocks MachineÂ
1. Value clients, guarantee equipment quality and answer clients' questions anytime and anywhere.
2. Customizing machines according to clients' inquiry , such as different design, different brand parts, different colors, more function,etc.Â
3. Engineers go to clients' factory in time for installation , training and trial production .Â
4. More spare parts are given to clients for free to ensure the factory working without suddenly stop.
5. 1 year free warranty, Lifetime technical service support.Â
7.Company Information
 1,Established in 1988, with the 27 years of development ,Fangyuan has development more than 10 offices inside and outside of China, with over 700 staff and covered 100,000 sqm2 workshop.
2,Yearly around 2200 sets machines and 2000 sets EPS moulds outputs, which keep Fangyuan as the leading EPS,XPS,EPP Machinery manufacturer in China. Â
3,Fangyuan is the first drafter of National Standard of EPS machinery in China; And obtained the ISO9001-2008 and European Standard CE certification.
Turning Parts:
Turning the workpiece in a lathe using the method of cutting tool rotation processing workpiece. Turning processing cutting is mainly composed of workpiece and not provide tools. Turning is the most basic, the most common method of cutting, occupies a very important position in the production. Turning for processing rotary surface, a large part of workpiece with rotating surface turning method of processing can be used, such as the external cylindrical surface, inside and outside the cone face, face, groove, screw and rotary forming surface, the tool is mainly used tools. Turning precision is generally it11-it7, some can reach IT6, surface roughness Ra 12.5-08um. can be achieved by Turning Parts, we call turning parts, there are many kinds of turning parts, most famous is via hard turning to maintain the thermal stability of the parts.
Category:
Based on different facilities(CNC facility) to do the turning process,CNC turning parts included Lathing Parts,milling parts,Grinding Parts;
Basically,we can realise it on different raw material,like copper alloy,steel,and aluminium alloy.
Concerned Factors:
(1) The biggest problem is to use or without cooling liquid. For interrupted cutting parts such as gears, the best use of "dry turning", otherwise the thermal shock feed and withdrawal knife is likely to cause the blade to rupture. As for the continuous cutting knife head, high temperature produced in dry turning process to toughening (softening) the pre cutting area, thereby reducing the hardness of the material to make it easy to cut. This phenomenon shows that the stem cutting speed increase is good. At the same time, no coolant cutting method has obvious cost advantages. (2) Layer whitening whitening scald layer (heat affected zone) "may be a dislike to appear in hard turning and grinding operation, namely in the material surface to form a layer of invisible to the naked eye is very thin (typically 1 m) crust. The formation of albino layer in the hard turning process, usually because of blade Passivation causes too much heat to the inner parts. Often whitening on bearing steel form, and it is very harmful to the bearing ring like need to withstand high contact pressure parts, with the passage of time, the albino layer may stripped and lead to bearing failure.
(3) Machine:stiffness determines precision hard turning. Nearly 15 ~ 20 years of manufacturing machines in the almost all have good rigidity, enough to withstand hard turning. In many cases, the overall condition of the machine is largely over the use of life is more important, the general maintenance The opening of the bed can also be used for hard turning. In order to increase the rigidity and damping characteristics for hard turning machine, hatey characteristics of many advanced machine tool for the machining center, including polymer composites reinforced with a spring clip (the spindle support near the workpiece) is directly matched with the spindle and hydrostatic guideway system. The maximum rigidity means a tool to reduce vacant, and extending parts out, and cancel the adjustable gap plate and gasket, its goal is to keep all parts as close as possible to the turret.
(4) Process:because of the heat generated by hard turning most chips away, before and after the processing of chip inspection You can find the whole process is coordinated. Continuous cutting, the chip should be blazing orange, and like a ribbon like flowing out. If the chip after cooling by hand pressure fracture, shows that cutting heat is normal.
(5) Blade:cubic boron nitride (CBN) inserts the price is expensive, but the most suitable for the hard cutting blade CBN.Cbn blade can keep unchanged in the positioning of intermittent cutting process, to provide a safe tool wear rate in continuous cutting process. When using the hard turning process reasonable, except in the control of CBN blade diameter tolerance is not better than grinding, other properties are second to none.
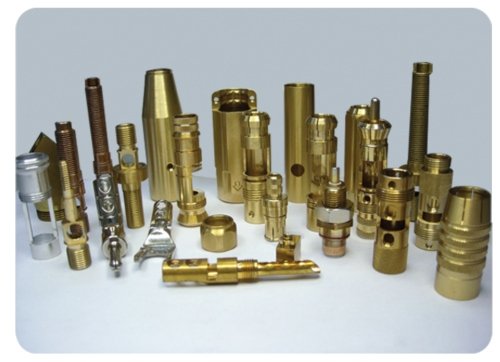
Turning Parts
Turning Parts,Lathing Parts,Milling Parts,Grinding Parts
VESTA Motoring Ltd , http://www.vesta-industry.com