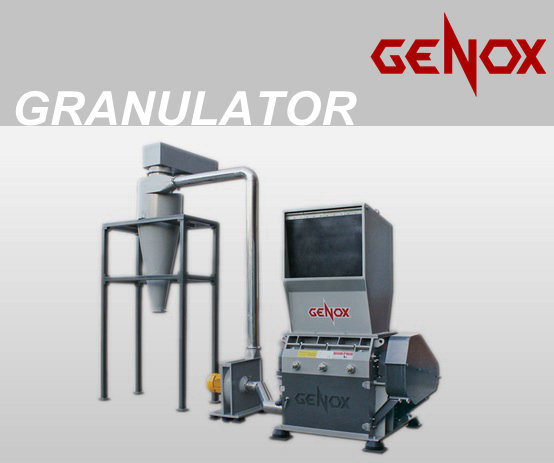
GENOX Granulator
GC Series Granulators are high speed granulation machines designed especially for theÂ
efficient size reduction of various materials in a single pass. These machines are ideal for
processing a multitude of materials including plastics, rubber, fibers, copper cable and light
non-ferrous metals amongst others.Â
Â
These machines are characterised by their high efficiency, reduced power consumption
and low noise, sound proof designs.
Â
Driven by a powerful motor, the rotor blades spin at high speed, cutting the feed material
into smaller pieces as they interact with the two rows of fixed blades.
Â
For processing different materials, special rotor designs, including V,S,C $ CSÂ
configurations can be specified. Manufactures from heat treated AISI D-2 high alloy material, the blades demonstrate excellent wear properties. The advanced,Â
precision machined rotor improves cutting efficiency and facilitates easy maintenance,
reducing down time during blade changes.

Specifications
Â
model | GC600 |
Dimension L X W X H(mm) | 1120×1330×1830 |
Hopper opening W X H(mm) | 560×500 |
Rotation diameter(mm) | Φ260 |
Rotor operation length(mm) | 600 |
Rotation speed(rpm) | 580 |
Standard screen (mm) | Φ12 |
Rotor knives (pcs) | 3×2 |
Counter knives (pcs) | 2×1 |
Drive power (kW) | 15 |
Weight (kg) | Approx 1000 |
Standard Features
product migration
components and Siemens PLC's
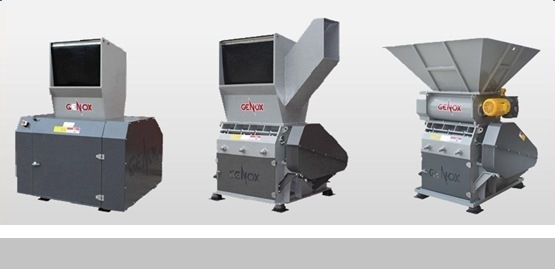
Company profile
Genox is a combined word of "Generating Oxygen" with a meaning of creating a better environment through new and innovative technology.Both the employees and management of Genox abide by this principle and constantly pursue the most effective, reliable and cost-effective solutions for the recycling of waste materials.
Â
Through extensive testing, seeking feedback from our valued customers and distributors, and working closely with our European engineering partners. Genox has developed an extensive range of technically advanced machinery for the processing of plastics, tires, and E-waste.
Â
Plastics shredding, granulation, and washing systems, including complete recycling plants, are the important part of the Genox product range. Single shaft shredders, two shaft shredders, granulators, washing tanks, dewatering centrifuges and other necessary equipment which can be customized on request allows us to offer bespoke proposals tailored to suit the requirements of each and every customer.Â
Â
Certification
Â
We awarded 50 utility model patents and 3 invention patents.
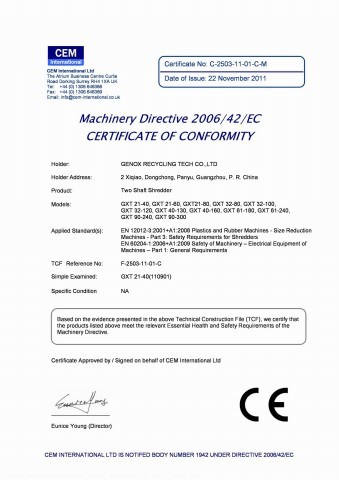
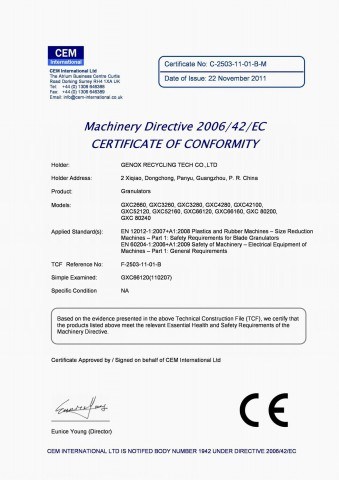
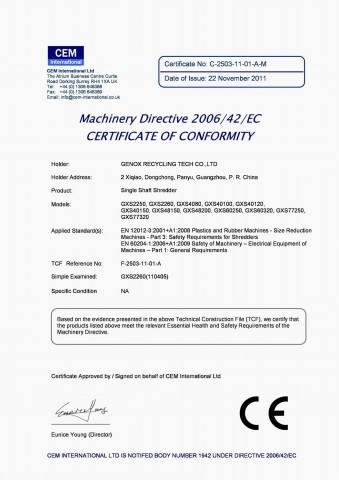
FAQ
1.Question:Will we provide pre-sale services ?
Answer:Genox consists of experienced specialists, we will offer a suitable solution according
 client's requirement in time.
2.Question:Is our after-sales service excellent ?
Answer:Genox's skilled technicians are available to assist with onsite installation,
commissioning & training on request. This will enable customers to optimize the performance of
their new plant. Customers will be briefed on all aspects relating to operation and maintenance
by a Genox technician. Dimensional drawings together with service requirements will be provided
prior to delivery of the equipment. This will allow the customer to prepare the site and allow
them to commence production in a timely fashion.
  Genox holds a adequately inventory of spare parts and their efficient service personnel will
ensure that any required part will be dispatched without delay. Delivery  of the spare parts
may be by air, sea or courier depending on the urgency of the situation. Customers are
encouraged to hold their own critical spare parts such as granulator blades and screens to
ensure optimal machine condition and performance.
Â
3.Question:Will we provide technical support ?
 Answer:Genox provides enough hardware resource especially for large-scale production lines,
clients can carry out installation, commissioning and acceptance before delivery.
Â
Contact Detail:Â
Telephone:86-20-66851346Â Â Â
Fax:Â 86-20-66851347
Â
Address:Â 2 Xiqiao, Dongchong Panyu, Guangzhou, Guangdong, China 511453
Welcome to contact us at any time We will reply you within 24 hours
In a large industrial Brick Making Machine, clay is taken from the quarry, and then carried by conveyor belt or truck/lorry to the main factory, although it may be stockpiled outside before entering the machinery. When the clay enters the preparation plant (Clay Prep) it is crushed, and mixed with water and other additives which may include breeze, a very fine anthracite that aids firing. This process, which is also known as pugmilling, improves the consistency, firing qualities, texture, and colour of the brick. From here, the processed clay can be extruded into a continuous strip and cut with wires, or put into moulds or presses (also referred to as forming) to form the clay into its final shape. After the forming or cutting, the bricks must be dried, either in the open air, in drying sheds, or in special drying kilns. When the bricks have been dried, they must then be fired or 'burnt' in a kiln, to give them their final hardness and appearance.
Brick Making Machine
Brick Making Machine,Clay Brick Making Equipment,Clay Brick Making Machine,Brick Making Equipment
Shandong Shine Machinery Co.,Ltd , http://www.sdshinemachinery.com