Description:
This radiator production line can be used in producing different specification radiators, with width among 535, 520, 480, 460, 320, 310 and center distance more than 500mm.
This machine has high automation degree, high forming quality, and high efficiency. The property of this machine has reached world-class quality.
The work flow of this line is as follows: Automatic decoiling-roll forming- hydraulic punching and cutting-spot welding-seam welding-panel head welding-head cutting-edge shearing-run-out.
The main components of the radiator production line are automatic decoiler, roll forming machine, leveler, oil press machine, press mould, series welding device, head cutter, edge shearer, product conveyer, pneumatic system, hydraulic system, and electric system, etc.
Properties:
Compared with similar lines, this radiator production line is fully automatic. Properties of its products have reached world-class quality.
This line has features of high production efficiency and low labor cost. This line can manufacture many different specification products. PLC controls all the welding procedures, and both welding quality and efficiency are very high.
Operation and Points That Need Attention:
The whole radiator production line is automatically controlled by PLC. Users can start the line to manufacture only by inputting product length.
Maintenance and Lubrication:
Users should regularly do lubrication for pneumatic device, and oil press machine, etc. Since there are many welding equipments in the line, users should often check working conditions of every equipment.
Packaging and Transportation:
This radiator production line adopts sea shipping by container and nude packaging.
Main Specification
Item | Data | |
Standard panel size | 310mm, 320mm, 460mm, 480mm, 520mm, 535mm, etc | |
Panel length | 500-4000mm | |
Length tolerance | ±1.0mm | |
Panel bearing pressure | Positive pressure≥ 0.15Mpa, negative pressure ≥ 133Kpa, without deformation | |
Panel material | ST12, SPCC, DC01 cold rolled steel, 1.0-1.2mm | |
Total power | Approx 315KW | |
Total line dimension | 46.5m X 3.5m | |
Oil fluits size | Steel thickness 1.0mm | ≥ 11mm |
Steel thickness 1.2mm | ≥ 11.5mm | |
Number of oil fluits | Panel 310mm, 320mm | 3 |
Panel 460mm, 480mm | 5 | |
Panel 520mm, 535mm | 6 | |
Input coil width | Panel 310mm | 325mm |
Panel 460mm | 475mm | |
Panel 520mm | 535mm |
Machine photos
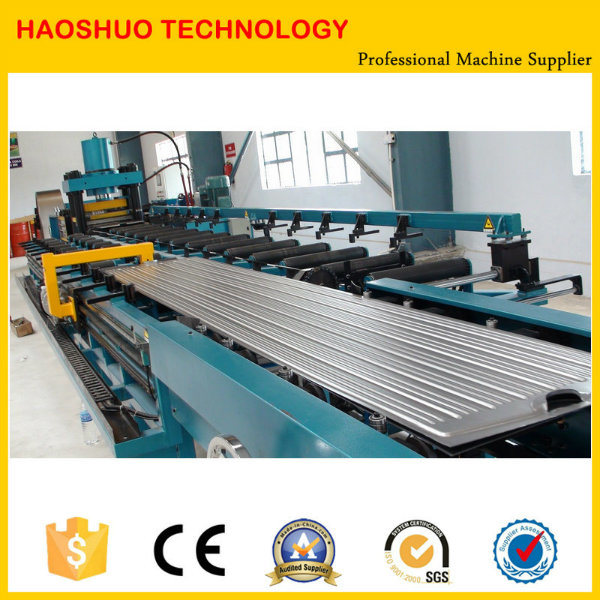
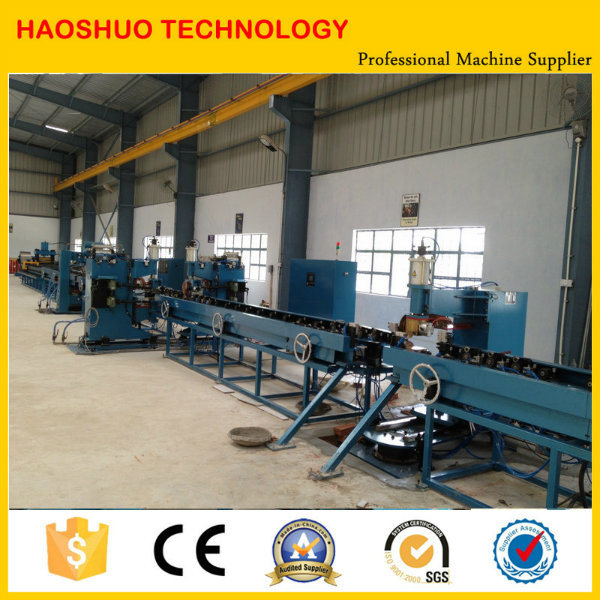
 Transformer Panel Radiator Production Line
Description:
This radiator production line can be used in producing different specification radiators, with width among 535, 520, 480, 460, 320, 310 and center distance more than 500mm.
This machine has high automation degree, high forming quality, and high efficiency. The property of this machine has reached world-class quality.
The work flow of this line is as follows: Automatic decoiling-roll forming- hydraulic punching and cutting-spot welding-seam welding-panel head welding-head cutting-edge shearing-run-out.
The main components of the radiator production line are automatic decoiler, roll forming machine, leveler, oil press machine, press mould, series welding device, head cutter, edge shearer, product conveyer, pneumatic system, hydraulic system, and electric system, etc.
Properties:
Compared with similar lines, this radiator production line is fully automatic. Properties of its products have reached world-class quality.
This line has features of high production efficiency and low labor cost. This line can manufacture many different specification products. PLC controls all the welding procedures, and both welding quality and efficiency are very high.
Operation and Points That Need Attention:
The whole radiator production line is automatically controlled by PLC. Users can start the line to manufacture only by inputting product length.
Maintenance and Lubrication:
Users should regularly do lubrication for pneumatic device, and oil press machine, etc. Since there are many welding equipments in the line, users should often check working conditions of every equipment.
Packaging and Transportation:
This radiator production line adopts sea shipping by container and nude packaging.
Main Specification
Item | Data | |
Standard panel size | 310mm, 320mm, 460mm, 480mm, 520mm, 535mm, etc | |
Panel length | 500-4000mm | |
Length tolerance | ±1.0mm | |
Panel bearing pressure | Positive pressure≥ 0.15Mpa, negative pressure ≥ 133Kpa, without deformation | |
Panel material | ST12, SPCC, DC01 cold rolled steel, 1.0-1.2mm | |
Total power | Approx 315KW | |
Total line dimension | 46.5m X 3.5m | |
Oil fluits size | Steel thickness 1.0mm | ≥ 11mm |
Steel thickness 1.2mm | ≥ 11.5mm | |
Number of oil fluits | Panel 310mm, 320mm | 3 |
Panel 460mm, 480mm | 5 | |
Panel 520mm, 535mm | 6 | |
Input coil width | Panel 310mm | 325mm |
Panel 460mm | 475mm | |
Panel 520mm | 535mm |
Machine photos
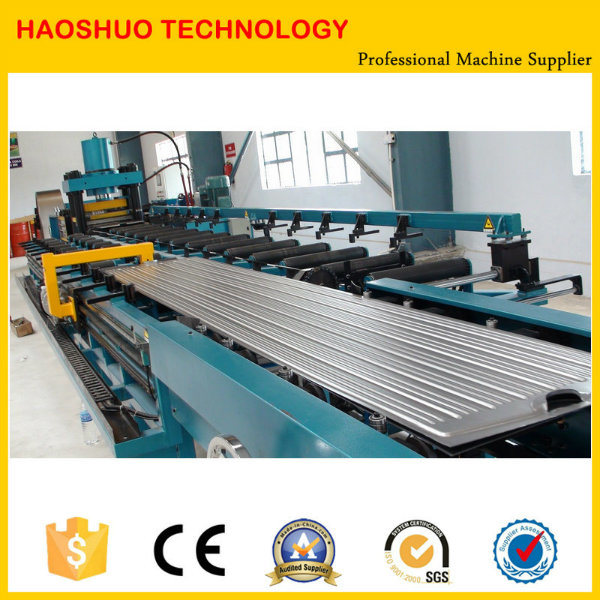
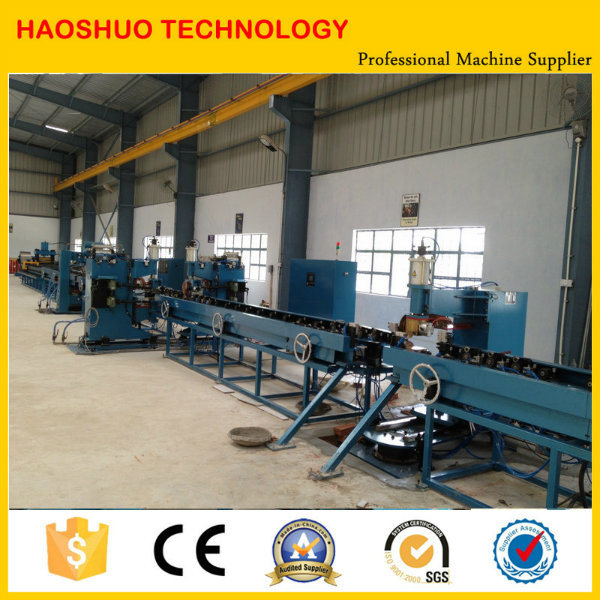
Â
This series of permanent-magnet synchronous gearless traction machines is directly driven by a low-speed, high-torque, 3-phase permanent magnet synchronous motor, and has the advantages of low energy consumption, low noises, no pollution, and little maintenance.
By using flat frame structure with three mounting surfaces, this series of traction machines can be installed on bottom floor or any middle positions or on the top of shaft way.
These traction machines can be arranged for providing upward traction or downward traction, and have remote manual brake release function. Wrap angle of the traction machines can be only 180°.
Standard Gearless Traction Elevator, Gearless Elevator Traction Machine, Gearless Elevator Machine, Gearless Traction Motor
Gearless Traction Machine,Gearless Traction Elevator, Gearless Elevator Traction Machine, Gearless Elevator Machine, Gearless Traction Motor
Ningbo Xinda Elevator Traction Technology Co., Ltd. , https://www.xinda-elevator.com