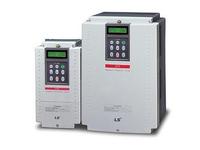
"Five" policy to promote the development of the inverter <br> <br> drive from research and development to date, frequency conversion technology in many production processes have achieved significant energy savings. The National "Twelfth Five-Year Plan for Energy Saving and Emission Reduction" requires the implementation of energy-saving renovation projects. Energy-saving of the motor system is one of the major projects. It is required to implement energy-saving transformations such as variable frequency speed control, permanent magnet speed control, and reactive power compensation for the motor system. Operation and control improve the overall operating efficiency of the system. The plan proposes that the operating efficiency of the motor system in 2015 will be 2 to 3 percentage points higher than that in 2010, and the energy saving capacity of 80 billion kilowatt-hours will be formed in the 12th Five-Year Plan period.
Therefore, since the "Twelfth Five-Year Plan", energy-saving and environmental protection, as the core of China's industrial economic development, has pointed out the direction for the sustainable development of China's industry, and at the same time, it has effectively promoted the sustainable development of China's inverter industry, so that China's inverter industry. Constantly expanding the market share of the industry and relying on its strong development power has become an important starting point for the development of China's industrial economy.
The frequency conversion energy saving is mainly used in applications where the change of rotational speed of the AC motor is required to change the driving mechanical characteristics so as to meet the requirements of the production process, and is mostly applied to fans and pumps. When the motor can only be operated at rated speed, its drive machinery can only operate at a certain rated speed.
When the production process requires adjustment of process parameters, the flow rate can only be forced to change by increasing (decreasing) the system resistance method, and the motor is always running under rated conditions, resulting in waste of electrical energy. For example, the conventional speed regulation method for fans, pumps and other equipment is to adjust the amount of air supply and water supply by adjusting the baffle and valve opening of the outlet (or inlet). In addition to the power consumption, the system accessories are also increased, and the number of The probability of system failure. When using variable frequency speed regulation, if the flow requirements are reduced, the requirements can be met by reducing the pump or fan speed.
In a comprehensive view, the inverter mainly achieves energy-saving effects through power factor compensation and soft-start. In terms of power factor compensation, the reactive power will increase the line loss and heat of the equipment. In addition, the reduction of the power factor leads to the reduction of the active power of the grid. Among the large number of reactive power consumption lines, the equipment is inefficiently used and wastes. After the frequency converter is used, the internal filter capacitor of the inverter acts to reduce the reactive power loss and increase the active power of the power grid.
In soft start energy saving, the hard start of the motor will cause serious impact on the power grid, and at the same time, the capacity requirement of the power grid is also too high. When the large current and vibration are generated during startup, the damage to the baffle and the valve is extremely great, and the use of the equipment and pipelines is great. Life is extremely unfavorable. The use of the soft-start function of the inverter will start the starting current from zero, reduce the impact on the grid and the requirements for the power supply capacity, extend the service life of the equipment and valves, and thus save the maintenance cost of the equipment.
However, it should be noted that the use of frequency converters should avoid the problem of "small horse-drawn carts." The reason for this problem is based on the limitations of the working conditions at the time of production design, so that the design and installation save money. In many places, the frequency conversion power is less than the rated power of the motor. However, with the development of technology and the change of production conditions, the problem of "small horse-drawn carts" inevitably arises, causing the inverter to fail to operate normally.
Therefore, in the trial period of the inverter device, in order to prevent problems, detection and adjustment should be conducted in advance to avoid the above problems. In addition, after 6 years to 10 years of normal use of the inverter, it is easy to enter the high failure period. Faults such as burn-out of components, frequent failure of the components, frequent operation of the protection function, etc. often occur, which seriously affect their normal operation.
Energy-saving inverter selection of 10 major principles <br> <br> Meanwhile, in the selection of energy-saving inverter speed or, should adhere to the following 10 principles as a prerequisite for the decision scheme. If the local electricity price is high, the economic benefits will be even greater at the same power savings. This is an inevitable consideration.
1) There are certain conditions for the inverter to save electricity. Under the conditions that do not affect the use, after properly changing the parameters of operating conditions, the energy consumed by the irrational operating parameters can be saved, and it can be converted from general operation to economic operation.
2) The frequency must be reduced in order to save energy. The larger the decrease, the more energy saved. Without reducing the frequency, the inverter cannot, in principle, save power.
3) It depends on the motor load rate. When the load rate is between 10% and 90%, the energy saving rate is at most about 8% to 10%. The low load rate corresponds to a higher power saving rate. However, the rate of reactive energy saving is about 40% to 50%, which is excluding electricity charges.
4) It is related to the reasonableness of the original operating condition parameter values. For example, the pressure, flow rate, speed, etc., are related to the magnitude of the adjustable amount. If the amount of adjustment is large, the energy saving rate is high, otherwise it is the opposite.
5) It is related to the adjustment method originally used. The use of imported or exported valves to adjust the operating parameters is not economical. If it is changed to speed control, it is economically reasonable. After the inverter is used to adjust the speed, the operation method can be adjusted by more than 20% to 30%.
6) It is related to the original speed control method. For example, the original slip motor speed, due to low speed efficiency, especially in the middle and low speed, the efficiency is only 50% or less, it is not economical, after the inverter speed control, this part of the power saved. At present, most of the industries such as light industry, textiles, papermaking, printing and dyeing, plastics, and rubber still use slip motors. Therefore, the use of frequency converters to achieve energy saving and technological transformation work are urgent tasks.
7) It relates to the working mode of the motor. For example, the power consumption of continuous operation, short-time operation, and intermittent operation is different.
8) It depends on the length of time the motor is started. For example, if you turn on the computer for 24 hours a day, the power saving will be large for 365 days a year, and vice versa.
9) It depends on the power of the motor itself. At the same electricity saving rate, the large power saving value is large, and the economic benefit is large. Even if the energy saving rate is lower than that of a small power motor, the actual profit is large.
10) It is related to the importance of the production process of the unit. First of all, it is necessary to select products with high power consumption, high product cost, and current use of speed control methods that are not economical and reasonable. Each of them should be reconstructed. Switching to frequency converters will have the effect of achieving immediate results and doing more with less.
Biomass Wood Fired Thermal Oil Boiler
YLW series of coal/biomass fired thermal oil boilers use coal or biomass as the fuel and thermal oil as the medium, and force the medium to conduct liquid phase circulation by the circulating oil pump. The boiler consists of the body above and the grate below.
The radiation heat transfer section of the boiler body adopts the double square shaped compact coil structure, the convection heat transfer section adopts the S shape multiple passes heat transfer. A high efficiency air preheater is equipped at the tail of the boiler, it can absorb heat and reduce exhaust gas temperature. After the fuel is fully burned in the combustion chamber, most of the heat is absorbed by the radiation heating-surface, the high temperature flue gas enters the convection heating surface and transfer the heat. After it comes out of the boiler, the air that is needed by boiler combustion is heated in the air preheater.
Then it passes the dust collector and is drawn by the I.D. fan to be discharged into the atmosphere through the chimney.
Biomass Wood Thermal Oil Boiler,Industrial Wood Fired Thermal Oil Boiler,Industrial Biomass Fired Thermal Oil Boiler,Biomass Fuel Thermal Oil Boiler,Wood Fuel Thermal Oil Boiler
Henan Yuanda Boiler Co., Ltd. , https://www.industrysboiler.com