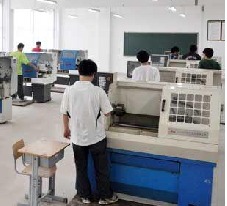
Compared with machine tool OEMs, there are a large number of domestic machine tool accessory companies. Except for a few state-owned enterprises, most companies have smaller scale problems. There is a certain level of difference in the accuracy of equipment and equipment performance of production companies. At present, there are major problems in the machine tool accessory industry in the country. There is insufficient investment in new product development, the level of product sales convergence needs to be further improved, and the producers’ awareness of product quality needs to be strengthened and the adjustment of high and low-end product policies must be strengthened.
Technological progress is also fast. However, compared with foreign counterparts, the difference is still very large. The main reasons are: First, the development of the industry is related to the past political environment. In recent years, the scale of China's machine tool component manufacturers has developed rapidly. In the past, the level of state support was not enough, and the idea of ​​quick success for enterprises was serious, leading to heavy hosting and light components. The second is that the amount of scientific research is low and the foundation is thin.
Some key component areas, for example. Some companies can also do it, but use ordinary machine tools to make high-precision functional components, these products can also be used on some high-end CNC machine tools, but the accuracy of the stability and adherence can not be, coupled with the raw materials, problems and processes Level problem. Foreign advanced components can be used for three years without replacement, while domestic components may only be replaced in one and a half years. This is also the reason for the low market share of domestically produced functional components.
Various policies have also greatly encouraged the development of machine tool accessories companies. The financial crisis has had a profound impact on China. Encouraging to seek development from time to time during the crisis, due to the impact of the economic crisis, the overall decline in the machine tool accessories market, and the stricter requirements of users, coupled with the competitive pressures of major foreign machine tool companies, the domestic related enterprise market is facing a great risk . Ao Li Machine Tool Network believes that it is necessary to complete the revitalization planning goals of the Chinese machine tool industry in the next three years. That is, the domestic market share of domestic machine tools will increase to more than 70%, and the occupation of CNC machine tools will increase to more than 40%. It will be necessary to increase the number of domestic CNC machine tools. Matching rate, this is the biggest bottleneck restricting the development of machine tools.
The domestic market share of domestic machine tools has increased to more than 70%, and the market share of CNC machine tools has risen to more than 40%. This is an arduous goal. The key components and accessories determine the development of the mainframe. Only the key components and accessories have been developed to the next level. The self-sufficiency rate of key functional components has been improved to form a batch of large-scale CNC machine tool manufacturers with strong international competitiveness. It can be regarded as a powerful country. At present, it is only a manufacturing power.
For example, a touch sensor for detecting the position and a plurality of sensors are used during the production of the machine tool. Proximity switches, piezoelectric sensors for detecting pressure, piezoresistive sensors and capacitive sensors, rare thermoelectric sensors based on platinum and copper, thermistor sensors based on semiconductor data, and thermocouple sensors Wait. On CNC machine tools, temperature sensors are used to detect the temperature so that the temperature compensates for overheating. The machine tool production process is based on sensors and other components, and it also puts higher requirements on sensors.
At present, the Chinese automobile industry is the main body of machine tool consumption, according to statistics. Machine tools account for about two-thirds of the total investment in fixed assets of automakers. Among them, the demand for machine parts for auto parts processing is about ten times larger than that for automakers, and it accounts for about 70% of the demand for machine tools in the automotive industry. Three years later, it was received by China. With the large number of idle production capacity and large-scale mergers and reorganizations in the automotive industry, the demand for machine tools in China's automotive processing industry will gradually decline, and the demand for machine tools will also be more environmentally friendly and efficient. The increase in demand for machine tools has further increased the requirements and quality requirements of various sensors such as proximity switches, speed sensors, and pressure sensors.
The development of numerical control systems, functional components, and cutting tools has shown a serious lag with respect to the development of mainframes. There is also a serious irrationality in the industrial chain and industrial structure of the entire machine tool industry in China. Compared with the host computer, CNC systems, functional components and tools are not satisfactory in terms of "strong" and "large", and there are still great differences between the current world level and even the companies in Taiwan. This restricts the sustainable development of China's high-end CNC machine tools at a certain level, and must arouse the attention of relevant leaders.
Weihai Xinghaiyuan Fishing & Netting Tackle Co.,Ltd. , https://www.yesonagri.com