I. Introduction
Overview of Laser Cutting Technology
Laser cutting technology has revolutionized the field of precision metal processing and manufacturing. By using a focused laser beam to cut, melt, or vaporize materials, laser cutting offers unparalleled precision, speed, and versatility, making it an indispensable tool in various industries such as aerospace, automotive, electronics, and medical device manufacturing.
The efficiency of laser cutting stems from its non-contact process, which minimizes material deformation and ensures high-quality edges. Modern laser cutting machines are equipped with sophisticated control systems that allow for complex shapes and intricate designs.
These machines can cut through a range of materials including metals, plastics, glass, and composites, accommodating diverse manufacturing needs.
Importance of Proper Laser Cutting Machine Training
Despite the advanced capabilities of laser cutting machines, the mastery of this technology requires comprehensive training. Proper training ensures that operators understand both the technical and safety aspects of laser cutting, which is crucial for maximizing productivity and maintaining a safe working environment.
Operators must be familiar with the setup, calibration, and maintenance of the machines, as well as the specific software and control systems used to operate them. Additionally, knowledge of material properties and preparation methods is essential for achieving optimal cutting results.
Through systematic training, operators can develop the skills needed to troubleshoot issues and achieve consistent, high-quality output. Moreover, proper training mitigates the risks associated with operating high-powered lasers.
Safety protocols and emergency procedures are critical components of all training programs, aiming to protect operators from potential hazards such as laser radiation, electrical shocks, and fire hazards.
In essence, well-trained personnel not only enhance operational efficiency but also contribute to a culture of safety and continuous improvement within the organization.
As laser cutting technology continues to evolve, ongoing education and training become vital for keeping up with the latest advancements and maintaining a competitive edge in the industry.
II. Pre-Training Preparation
Effective pre-training preparation is paramount to ensure a successful learning experience for laser cutting machine operators. This preparatory phase encompasses several key elements designed to set a solid foundation for the comprehensive training that follows.
Prerequisites for Training
- Required Knowledge and Skills: Aspiring laser cutting machine operators should have a basic understanding of mechanical engineering principles and familiarity with computer-aided design (CAD) software. Knowledge of different materials and their properties, especially metals, will be advantageous. Basic mathematical and technical comprehension is also important for grasping the operational logic of laser cutting machines.
- Necessary Safety Equipment: Safety is a priority when working with laser cutting machines. Prior to beginning training, operators must be equipped with personal protective equipment (PPE), such as laser safety goggles to protect against harmful laser radiation, heat-resistant gloves, and protective barriers for potential fire hazards. Additionally, understanding the placement of emergency stops and ventilation requirements is crucial for maintaining a safe training environment.
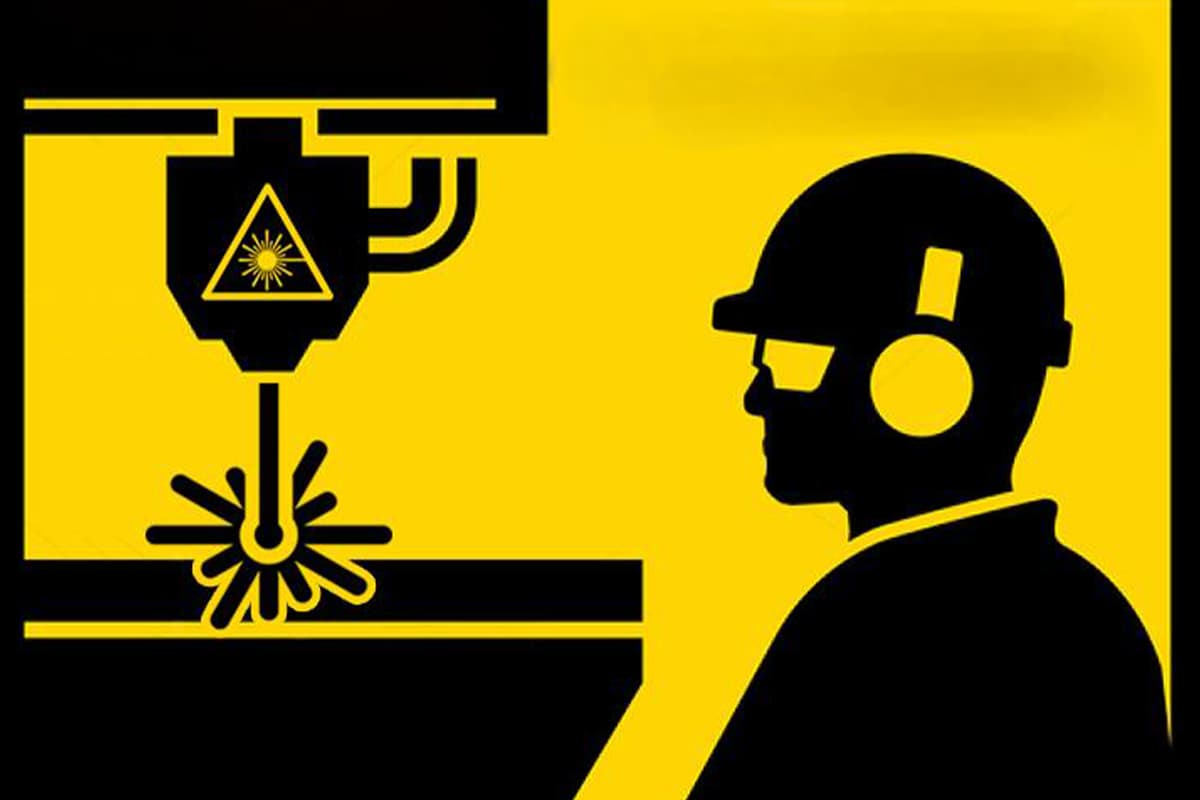
Choosing the Right Laser Cutting Machine
The selection of an appropriate laser cutting machine is critical and should align with the specific training needs of the organization or individual.
- Evaluating Different Models and Brands: Prospective trainees or organizations should evaluate different laser cutting machine models and brands, considering factors such as power output, precision, speed, and the types of materials they are capable of processing. The choice between CO2 lasers, fiber lasers, or other types is dictated by the intended applications and budgetary constraints.
- Determining the Appropriate Machine for Specific Tasks: The machine chosen should correspond with the specific tasks it will perform. For example, fiber lasers are often preferred for cutting metals due to their efficiency and precise cutting capabilities, whereas CO2 lasers may be more suitable for non-metal materials like plastics or wood. It is also worth considering machines with user-friendly interfaces for beginners or advanced features for experienced operators requiring complex operations.
III. Basic Training for Beginners
Initiating beginners into the realm of laser cutting requires a thoughtfully designed training program that bridges the gap between theoretical knowledge and practical skills.
This fundamental training phase aims to empower new operators with the confidence and competence needed to handle laser cutting machines effectively and safely. The key areas of focus in basic training include understanding laser cutting principles, hands-on machine operation, and basic troubleshooting.
Understanding Laser Cutting Principles
Before delving into hands-on machine operation, beginners must grasp the underlying principles of laser cutting technology.
- Basics of Laser Technology: Trainees will learn about the fundamentals of laser generation, the types of lasers used in cutting (such as CO2 and fiber lasers), and the mechanics of how a laser beam interacts with different materials to achieve precise cuts.
- Understanding Cut Quality Parameters: Operators must recognize factors that define cut quality, including edge smoothness, kerf width, and heat-affected zones. This knowledge aids in identifying optimal cutting conditions and achieving consistent results.
- Introduction to Laser Cutting Terminology: Familiarity with key terms used in laser cutting, such as focal length, beam divergence, and pulse frequency, ensures that trainees can effectively communicate and understand technical instructions.
Hands-On Machine Operation
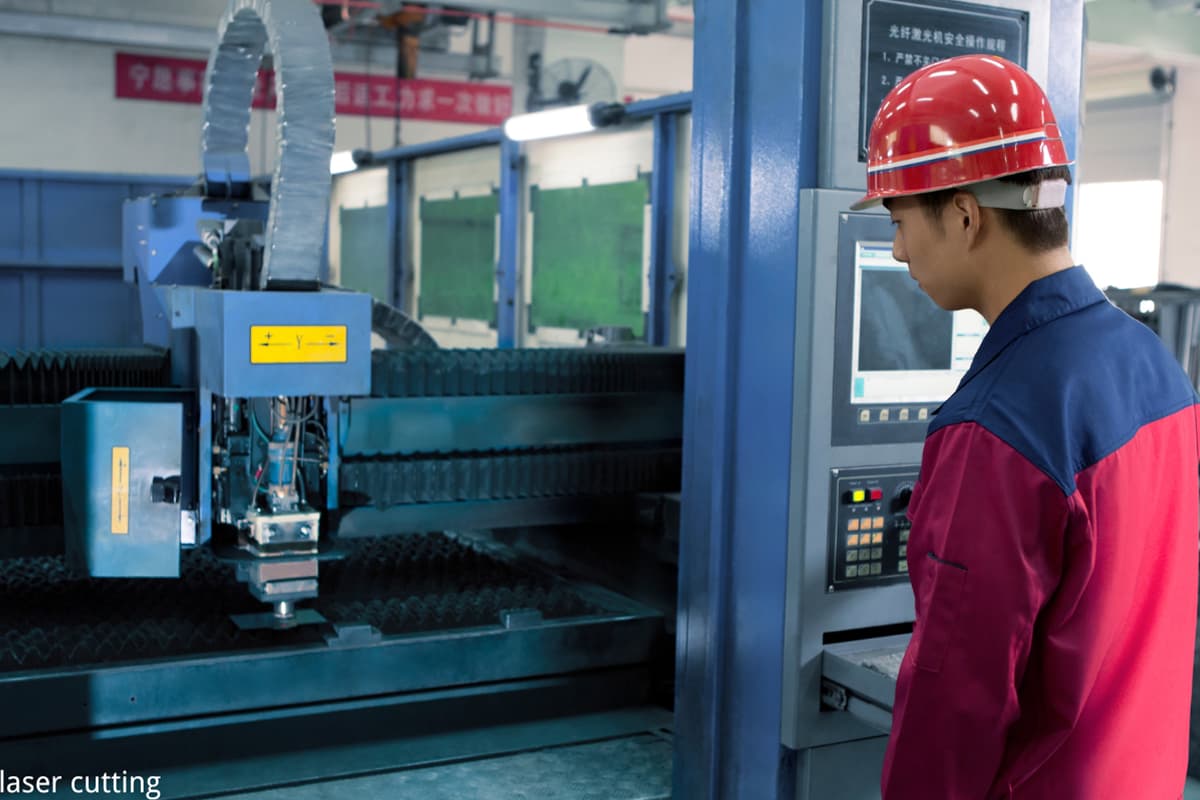
Practical, hands-on experience is essential for developing the skills necessary to operate laser cutting machines proficiently.
- Basic Machine Functions: Training will cover essential machine functions and controls, including power on/off procedures, laser head movement, focus adjustment, and basic navigation through the machine’s user interface.
- Executing Simple Cuts: Beginners will start with simple cutting exercises on basic shapes and materials. This helps them understand the relationship between machine settings (such as power, speed, and focus) and the resultant cut quality.
- Safe Material Handling: Proper techniques for loading and unloading materials, securing workpieces on the cutting bed, and ensuring materials are free of contaminants are crucial skills that will be practiced during training.
Basic Troubleshooting and Problem Solving
Equipping operators with troubleshooting skills is necessary to maintain smooth and efficient machine operation.
- Identifying Common Issues: Trainees will learn to recognize and diagnose common issues such as poor cut quality, misalignment, laser beam inconsistencies, and software errors.
- Basic Maintenance and Adjustments: Instruction on performing routine checks and adjustments, such as cleaning lenses, realigning the laser head, and ensuring proper cooling and ventilation, helps prevent technical problems.
- Emergency Procedures: Trainees must be well-versed in emergency shutdown procedures, handling machine errors, and quickly addressing any safety hazards that may arise during operation.
IV. Core Training Modules
The core training modules form the backbone of an effective laser cutting machine training program. These modules are designed to provide a structured and comprehensive learning experience, covering all essential aspects necessary for the safe and proficient operation of laser cutting machines.
Module 1: Safety Training
Safety training is the cornerstone of any laser cutting machine training program. Given the high-intensity laser beams and electrical components involved, operators must thoroughly understand and adhere to safety protocols to prevent accidents and injuries.
- Laser Safety Protocols: This includes education on laser classifications, understanding the risks associated with different laser types, and proper use of laser safety goggles and other protective gear. Trainees will learn about controlled areas for laser operations and emergency shutdown procedures.
- Handling and Preventing Hazards: Operators will be trained on identifying potential hazards such as flammable materials, reflective surfaces, and electrical risks. This module also covers fire safety measures, including the use of fire extinguishers and smoke detectors, as well as procedures to follow in case of laser-induced fires.
- Proper Ventilation and Waste Disposal: Understanding the importance of adequate ventilation to mitigate fumes and dust, and adhering to environmental standards for waste disposal of materials processed by laser cutting.
Module 2: Machine Setup and Calibration
Proper setup and calibration are critical for ensuring the machine's precision and efficient operation. This module covers the detailed processes of setting up the laser cutting machine and fine-tuning it for optimal performance.
- Initial Machine Setup: Training on installation procedures, including power connections, laser tube alignment, and software installation. Emphasis is placed on following manufacturer guidelines for a secure and accurate setup.
- Calibration Procedures: Detailed instruction on calibrating the laser head, adjusting focus, and ensuring the cutting bed is level. Trainees will learn how to perform diagnostic tests to verify and maintain machine accuracy.
- Routine Maintenance Checks: Regular maintenance is essential for machine longevity and consistent results. This aspect of the module will include daily, weekly, and monthly maintenance tasks such as cleaning lenses, checking coolant levels, and inspecting components for wear and tear.
Module 3: Software and Control Systems
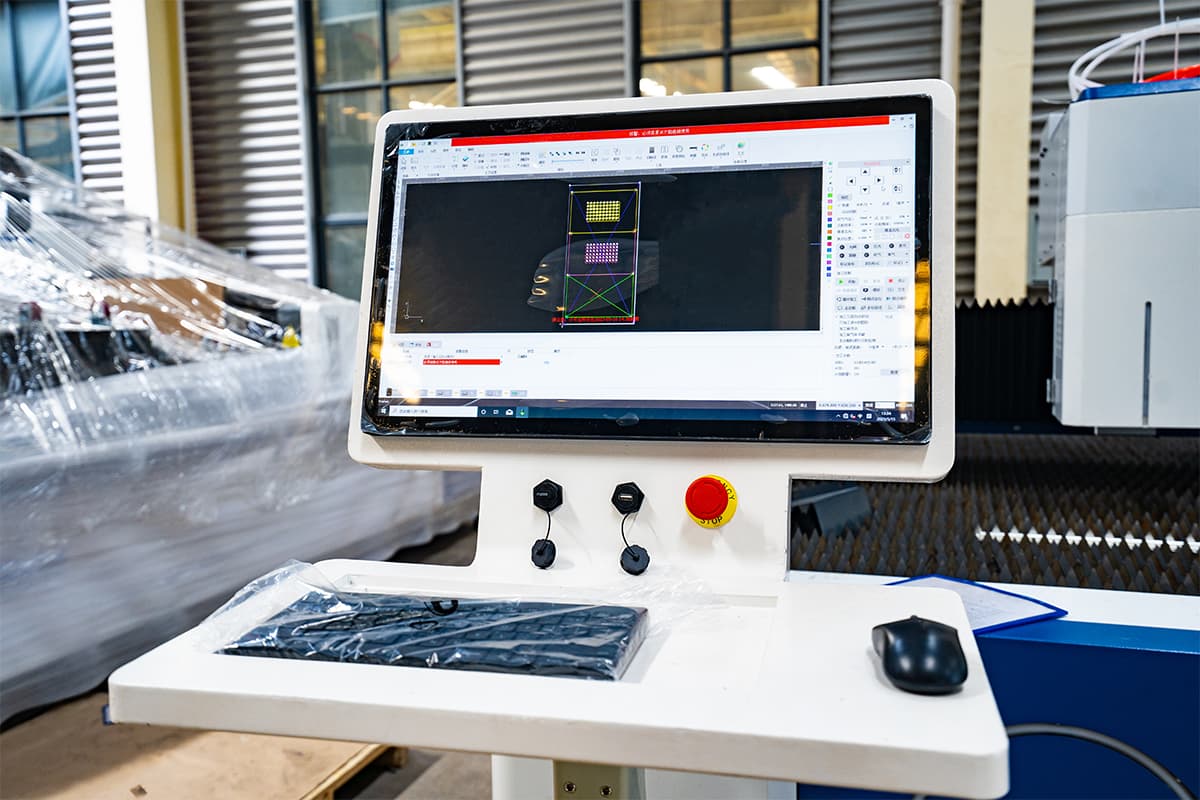
Understanding the software and control systems that operate laser cutting machines is vital for executing precise cuts and complex designs.
- User Interface Navigation: Training on navigating the machine's user interface, understanding control panel operations, and utilizing common features such as manual mode, automatic mode, and safety lockouts.
- CAD/CAM Software Integration: Detailed tutorials on using computer-aided design (CAD) and computer-aided manufacturing (CAM) software. Trainees will learn how to import and manipulate design files, set cutting paths, and optimize designs for efficient cutting.
- Programming and Troubleshooting: Basic programming skills for customizing machine operations and handling common issues. This includes setting parameters for different materials and techniques for troubleshooting software glitches or unexpected machine behavior.
Module 4: Material Selection and Preparation
The choice and preparation of materials significantly affect the quality of cuts and the efficiency of the machining process.
- Material Properties and Their Impact: Overview of different materials such as metals, plastics, and composites. Understanding their properties including thickness, density, and the impact of these factors on laser cutting parameters.
- Pre-Cutting Preparations: Training on material handling and preparation techniques such as cleaning, securing materials on the cutting bed, and pre-testing settings on sample pieces to avoid errors during actual cutting.
- Optimizing Laser Settings for Different Materials: Instruction on adjusting power, speed, and focusing parameters for various materials to achieve clean cuts, minimize waste, and reduce operational costs.
V. Advanced Training Techniques
Advanced training techniques for laser cutting machine operators are designed to elevate proficiency levels and enable the handling of complex tasks with precision and efficiency.
This section will delve into high-level functionalities, optimization strategies, and continuous improvement methodologies, critical for experts in the field who seek to enhance their capabilities and stay ahead of industry advancements.
Mastering Multi-Axis Cutting
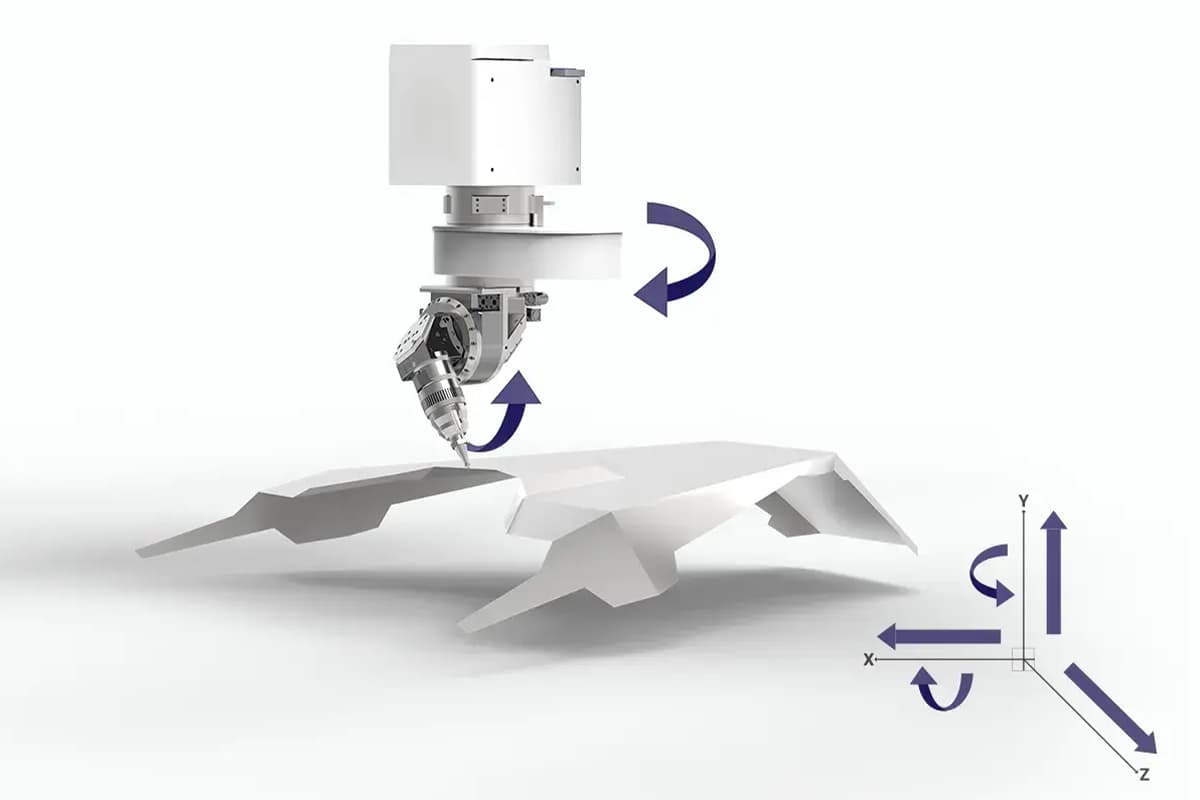
Multi-axis cutting expands the dimensional capabilities of laser cutting machines, allowing for more intricate and complex designs. This advanced technique requires a deep understanding of machine dynamics and software control.
- Understanding Multi-Axis Dynamics: Advanced training includes the study of the additional rotational and tilt axes, which enable the laser beam to approach the workpiece from multiple angles. Trainees must grasp the principles of 3D coordinate systems and the impact of multi-axis movement on cut quality and precision.
- Advanced Software Integration: Operators will learn to use sophisticated CAD/CAM software modules specifically designed for multi-axis operations. This includes setting up kinematic sequences, simulating multi-axis movements, and optimizing tool paths to minimize material wastage and enhance efficiency.
- Practical Applications and Techniques: Hands-on exercises in cutting complex geometries, such as curved surfaces and angled cuts, will be conducted. Operators will also be trained on specific techniques for managing material deformation and ensuring consistent focus throughout the cutting process.
Fine-Tuning for Precision and Quality
Achieving the highest levels of precision and quality in laser cutting necessitates the fine-tuning of machine parameters and a profound understanding of material interactions.
- Precision Parameter Optimization: In-depth training on adjusting laser power, pulse frequency, speed, and focus to achieve superior precision. Trainees will experiment with different settings to understand their effects on edge quality, kerf width, and heat-affected zones.
- Quality Control and Inspection: Advanced techniques for evaluating and ensuring cut quality involve using tools like optical microscopy and surface profilometry. Operators will learn to perform detailed inspections and implement feedback loops to continuously improve cutting processes.
- Adaptive Cutting Strategies: Implementing real-time monitoring and adaptive control systems to adjust parameters dynamically during the cutting process. This includes utilizing sensors and machine learning algorithms to predict and compensate for variations in material properties or environmental conditions.
Enhancing Cutting Efficiency
Efficiency in laser cutting operations is paramount for increasing productivity and reducing costs. Advanced training focuses on refining techniques to enhance overall operational efficiency.
- Nesting Optimization: Techniques for optimizing the layout of multiple parts on a single sheet of material to maximize material utilization. Software tools for automated nesting and strategies for reducing cutting paths and transition times between cuts are explored.
- Batch Processing and Automation: Training on setting up and managing batch processing routines, including the use of automated loading/unloading systems, conveyor belts, and robotic arms. Operators will learn to set parameters for unmanned operation, ensuring consistent performance over extended periods.
- Lean Manufacturing Principles: Applying lean manufacturing principles to laser cutting operations helps to eliminate waste and streamline processes. This involves value stream mapping, continuous improvement, and implementing Just-In-Time (JIT) production techniques.
Complex Material Processing
Advanced material processing techniques enable the cutting of challenging materials that require specialized knowledge and handling.
- Exotic and Composite Materials: Training includes the properties and cutting techniques for advanced materials such as titanium, carbon fiber composites, and high-strength alloys. Operators will learn to customize laser settings and cooling methods to handle these materials effectively.
- Microfabrication: Techniques for micro-scale laser cutting, essential for industries such as medical devices and electronics where precision at micron levels is critical. This involves understanding laser-matter interactions at small scales and using high-precision positioning systems.
- Multi-Material Stacking: Methods for cutting multiple layers of different materials simultaneously, optimizing the process for speed and consistency without compromising quality. This requires thorough knowledge of how different materials react to laser processing and how to balance power and speed settings accordingly.
Troubleshooting and Advanced Diagnostics
Expert-level troubleshooting and diagnostics are crucial for maintaining uninterrupted and high-quality operations.
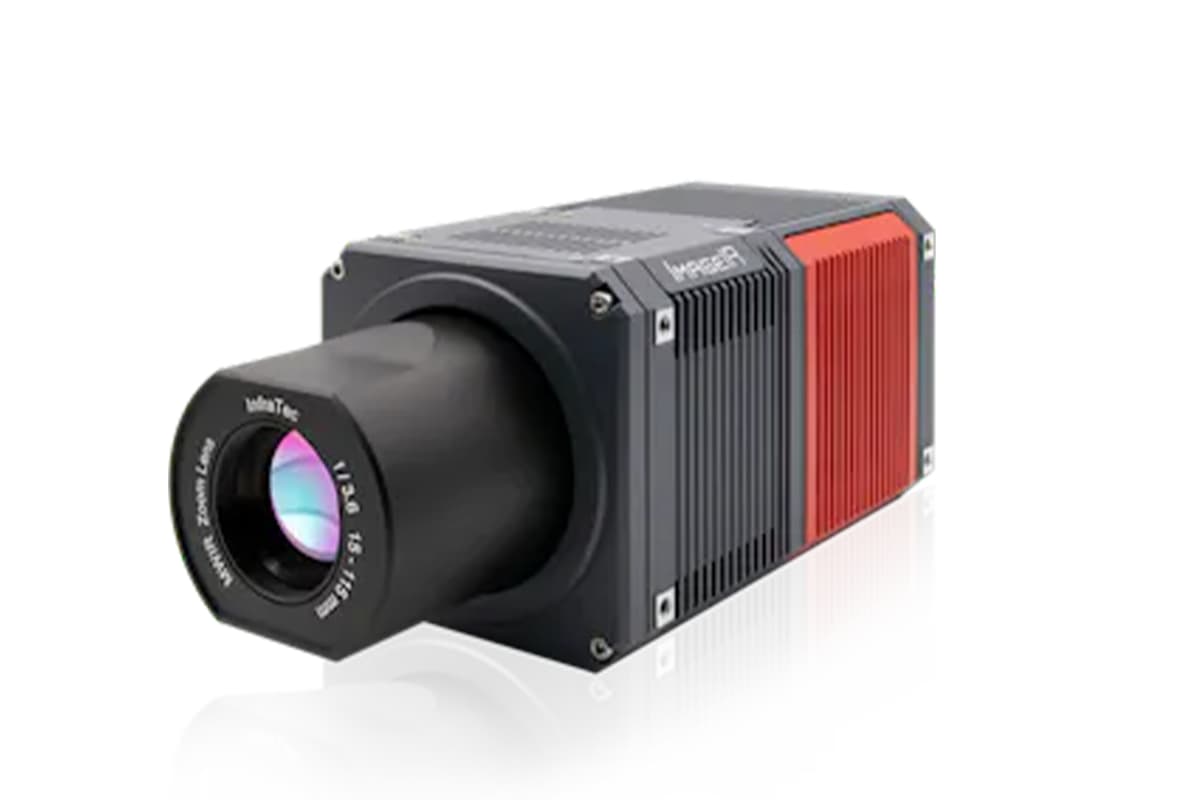
- Advanced Diagnostic Tools: Training on using advanced diagnostic tools like interferometers, beam profilers, and thermal imaging cameras to analyze and troubleshoot laser performance issues. These tools help in identifying problems with beam quality, alignment, and thermal effects.
- Predictive Maintenance Strategies: Implementing predictive maintenance techniques using data analytics and condition monitoring systems to anticipate and address potential machine failures before they occur. Understanding and applying these strategies help in maintaining high uptime and operational reliability.
- In-depth Case Studies: Studying real-world case studies of complex troubleshooting scenarios and the solutions implemented. This provides operators with practical insights and problem-solving approaches that can be applied in diverse situations.
Continuous Improvement and Certification
Continuous improvement is a fundamental aspect of advanced training, ensuring operators remain at the forefront of technological advancements and industry standards.
- Continuous Learning and Upgrading Skills: Encouraging participation in ongoing training programs, workshops, and industry seminars. Staying updated with the latest advancements in laser technology, software updates, and best practices through continuous education is emphasized.
- Pursuing Advanced Certifications: Guidance on obtaining advanced certifications from recognized industry bodies, which validate an operator’s expertise and can significantly enhance career progression. Topics covered include preparation for certification exams and understanding the criteria for various certification levels.
- Implementing Feedback and Innovation: Creating a culture that values feedback and innovation, where operators are encouraged to experiment with new techniques and share their findings. Collective brainstorming and collaborative initiatives are promoted to foster innovative solutions and continuous process enhancements.
VI. Certification and Continuous Learning
Certification and continuous learning are essential pillars for laser cutting machine operators aiming to achieve and maintain expertise in this technologically advanced field. These aspects ensure that operators remain proficient, adhere to industry standards, and are prepared for the evolving demands of laser technology.
The Importance of Certification
Obtaining certification in laser cutting operations validates an operator's skills and knowledge, enhances career prospects, and contributes to maintaining high industry standards.
- Recognition of Competency: Certification serves as an official acknowledgment of an operator's ability to handle laser cutting machines proficiently. It demonstrates to employers and peers that the operator has undergone rigorous training and met the industry criteria for skill and understanding.
- Enhancing Career Opportunities: Certified operators are often more attractive to employers due to their proven expertise. Certification can open doors to advanced positions, higher responsibilities, and potential salary increases within the manufacturing and technology sectors.
- Maintaining Industry Standards: Certification programs align with international standards, ensuring operators' practices comply with the latest safety, environmental, and operational protocols. This consistency across the industry enhances overall safety and quality.
- Types of Certification: Various certification levels exist, from basic operation to advanced specialty areas, each focusing on different aspects of machine operation, safety, and material handling. Operators can pursue certifications that match their level of expertise and areas of interest.
Pathways to Certification
Achieving certification involves different pathways, each tailored to the operator's level of experience and desired expertise.
- Foundational Certifications: These are designed for beginners and focus on the basic competencies needed to operate laser cutting machines safely and effectively. They cover fundamental skills in machine setup, basic material handling, and standard safety procedures.
- Advanced Certifications: Targeted towards experienced operators, these certifications cover complex operations, such as multi-axis cutting, exotic material processing, and advanced troubleshooting. Advanced certifications require a deeper understanding of both practical and theoretical knowledge.
- Specialty Certifications: These focus on niche areas within laser cutting, such as microfabrication, automation integration, or specific material applications. Specialty certifications help operators specialize in particular industry segments, enhancing their expertise and value.
The Role of Continuous Learning
As laser technology evolves, continuous learning ensures that operators remain at the forefront of industry developments, enabling them to leverage new advancements effectively.
- Staying Updated with Technology: Continuous learning involves regularly engaging with the latest technology trends, machine upgrades, and cutting-edge techniques in laser processing. This ongoing education helps operators anticipate and adapt to technological changes rather than react to them.
- Professional Development Workshops: Participating in workshops and seminars provides opportunities for hands-on experiences with new technologies and processes, facilitates networking with industry peers, and enhances problem-solving abilities through shared learning experiences.
- Online Platforms and Resources: E-learning platforms, webinars, and online courses offer flexible, up-to-date educational content that operators can access from anywhere. These resources are invaluable for learning new software, programming languages, and operational strategies.
Implementing a Learning Culture
Promoting a culture of continuous improvement and education benefits both individuals and organizations.
- Encouraging Innovation and Experimentation: A workplace culture that supports continuous learning fosters innovation. Operators are encouraged to experiment with new techniques and share their findings, leading to improved processes and products.
- Mentorship and Knowledge Sharing: Experienced operators can mentor less experienced colleagues, sharing knowledge and insights gained from years of practice. This mentorship accelerates learning and helps build a supportive professional community.
- Regular Feedback Mechanisms: Implementing a system for regular feedback and performance evaluations helps operators understand their strengths and areas for improvement. Feedback loops promote a cycle of continuous learning and development.
- Incentives for Continued Education: Organizations can encourage ongoing learning by offering incentives such as tuition reimbursement for courses, time off for professional development, or recognition programs for achieving certifications.
VII. FAQ
1. What are the most important safety measures to take when using a laser cutting machine?
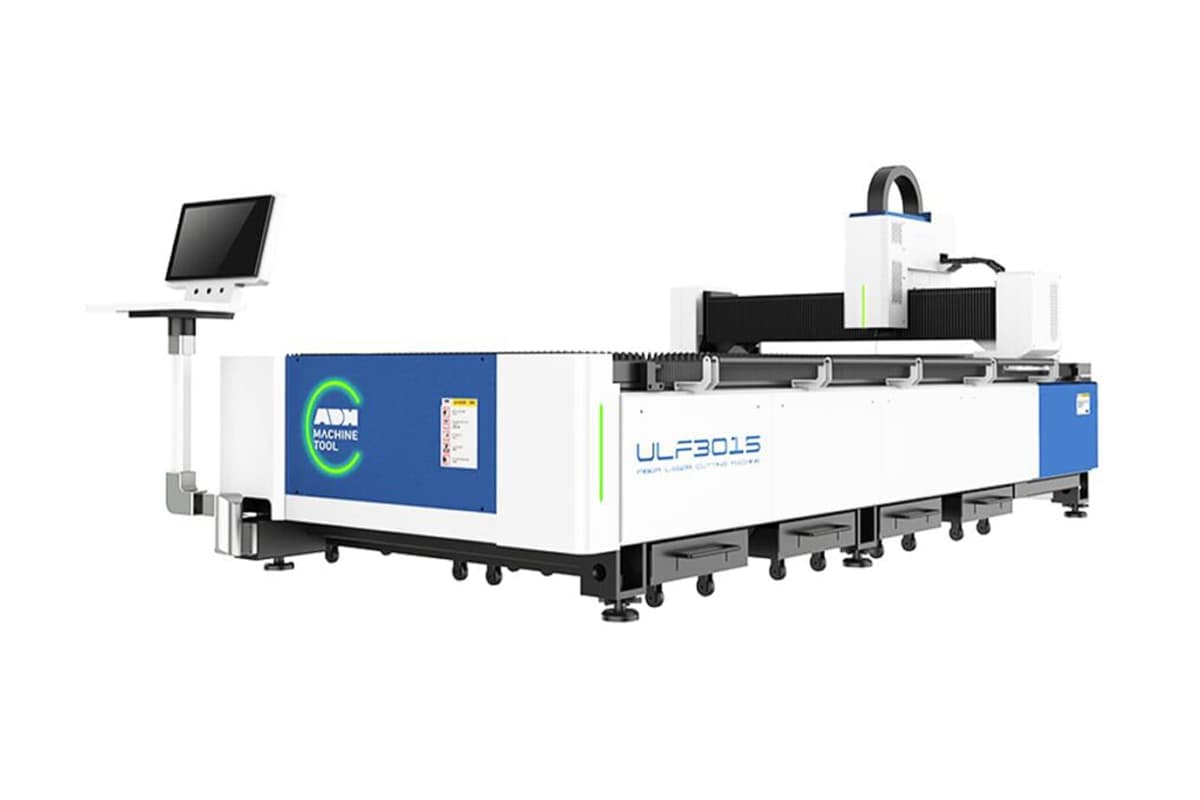
Safety is a top priority in laser cutting operations. Essential measures include wearing appropriate personal protective equipment, such as laser safety goggles and heat-resistant gloves. Operators should establish clear controlled areas and ensure proper machine grounding to prevent electrical hazards.
Additionally, adherence to emergency shutdown protocols and routine maintenance to prevent mechanical failures is crucial. Educating all personnel on fire safety measures, such as the use of extinguishers and ensuring adequate ventilation, further fosters a safe working environment.
2. What are the common materials that can be cut using a laser cutter?
Laser cutters can process a broad range of materials, including metals like steel and aluminum, and non-metals such as plastics, wood, glass, and composite materials. The choice of laser type—CO2, fiber, or Nd:YAG—affects cutting capabilities and efficiency.
Understanding the unique properties of each material, such as thickness and reflectivity, is crucial for determining appropriate laser settings and achieving optimal results.
3. How often should I perform maintenance on my laser cutting machine?
Regular maintenance schedules are vital to prolonging machine lifespan and ensuring consistent performance. Daily checks should include cleaning lenses, inspecting the cutting bed, and removing debris.
Weekly or monthly tasks might involve monitoring coolant levels, verifying beam alignment, and tightening mechanical components. Operators should follow manufacturer-specific guidelines and log maintenance activities to anticipate potential issues and minimize downtime.
Aluminum radiator for MAZDA,Radiator for MAZDA,Radiators for MAZDA
JIANGSU KALLER AUTO PARTS THCHNOLOGY CO.,LTD , https://www.jskaller.com