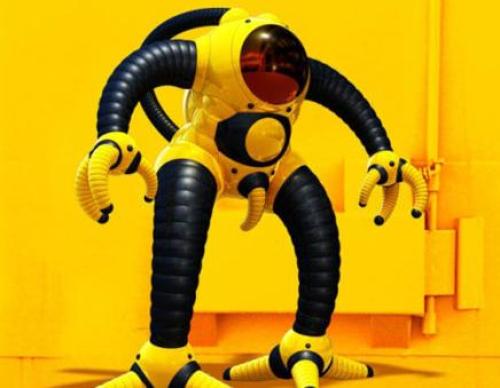
In recent years, one of the loneliness of the machine tool manufacturing industry has been reluctant to start cross-border playing industrial robots.
In the just-present machine tool exhibition, as long as the audience pays a little attention, the machine tool manufacturing companies involved in the robot have many new faces. For example, Dalian Guangyang Technology Engineering Co., Ltd. launched the first two robots at the exhibition.
One of the robots is good at handling, and the other is good at milling. It can three-dimensionally engrave wood and stone. According to Yu Dehai, chairman of Guangyang Technology, the end of the robot manipulator can not only weigh 166 kilograms or 210 kilograms of weight, but also can sculpt and cut stone, light aluminum, and wood with an error of no more than 0.01 millimeter.
Cross-border advantage
Among domestic machine tool companies, Koyo Technology is not the first wave of companies involved in the industrial robot market. Many years ago, Guangzhou CNC Equipment Co., Ltd., a professional supplier of CNC systems, began researching and developing industrial robots from 2007 onwards. By 2010, it has entered a small batch production stage.
At the machine tool exhibition, Guangzhou CNC took the RJ05, RJ10, RJ20 machine tool loading and unloading three-axis robots and RB20 side-hung robot unit unveiled. The former is applicable to the machining automation of vehicles, milling machines and other machine tools, and the structure is compact, and the price is only six-axis industrial robots. About half. The latter consists of an RB20 robot, a guide rail and a machine tool. The advantage of this unit is that it saves space, is more flexible than traditional truss robots, and can be equipped with multiple machine tools (more than 4 machine tools, the machine can swing).
The above two companies added Wuhan Huazhong Numerical Control Co., Ltd., and the three companies are all focused on the field of CNC system development or companies with special expertise in CNC control. The key application of industrial robots is motion control, so cross-border development can be described as a matter of course.
In fact, in addition to these, machine tool companies have also been eyeing this booming market. In the earlier interview with China Industry News, Zhu Zhiyang, chairman of the Youjia Group, made it clear that the industrial robot market was a field that You Jia must seize. The leading companies in the domestic machine tool industry, Shenyang Machine Tool, Dalian Machine Tool and others also made early preparations.
Of course, foreign brands aiming at the Chinese industrial robot market are also increasing their horsepower. For example, Jing Xirui, general manager of Beijing Fanuc Electromechanical Co., Ltd., said that in 2013, Fanuc sold 5,000 robots in China alone.
An analysis from the market statistics of the China Robot Network Data Research Center shows that in the Chinese robot market in 2012, the top ten sales are still dominated by foreign brands. Among them, Fanuc's 3,900 units, Yaskawa 3,850 units, KUKA 3,470 units, ABB 3,200 units, EDHI 2000 units, Panasonic 1,600 units, Xinsong 1,220 units, Kawasaki, Nachi and Hyundai are all selling at about 1,000 units.
FANUC, Yaskawa, Kuka and ABB are known as the Big Four in the international industrial robotics industry. In 2012, the total sales volume reached 14,470 units, accounting for 53.8% of the sales volume of the Chinese robot market. In 2012, the sales volume of local brand robots was only 2,252 units, with a market share of 8.7%.
In this analysis, the company that performed best in the domestic robot market in 2012 was Shenyang Xinsong Robot Co., Ltd., with sales of 1,220 units, followed by 400 units in Dongguan Kaifan and 200 units in Anhui Evert, Shanghai. Wodi 200 units, Guangzhou CNC 170 units.
To date, the data may have changed a lot. It is reported that the sales of Nanjing Estun, which has no name on the list, were already over 200 units in 2013, and Guangzhou CNC's target for 2013 is over 1,000 units.
The above data is nothing more than to prove that the application of industrial robots in various industries in China is still accelerating, and the companies involved in it have also accelerated the industrial layout. The reason why a large number of machine tool manufacturing companies intervene is because the relationship between machine tool manufacturing and robot manufacturing is very large.
In addition to the technical correlation, the machine tool as an industrial master machine also has a very large user base for contact, and its equipment can be sold together with industrial robots to realize an integrated solution.
It seems that machine tools have always been manufactured with precision and precision, but because of their characteristics, they can rarely achieve large-scale production. We know that the traditional machine tool companies not only have a complete accumulation of technical reserves, but also a large number of R & D personnel, in the relatively mature technology products, it is easier to find the right balance between quality, function and cost, and thus quickly achieve universal and Mass production, making efforts in the mid-market.
Doing large scale
The reason why it is suitable for entry into the mid-range market is that, in terms of the current situation, Europe and the United States still occupy a leading position in the comprehensive research level of industrial robot technology, and Japan’s industrial robots rank first in the world in terms of quantity and types. In addition, foreign-funded enterprises started early and the industry has formed a large-scale advantage. As a result, standardized processes have been formed in areas such as R&D and design, core parts and components, and have strong leading advantages.
I still remember that at one exhibition, a vision sorting robot developed by a company in Shenzhen could neatly discharge the screw loosely distributed in the barrel to a tray on the side, but the merchants watching it were not satisfied with it. “The precision is so poor. Hand grasping screws are not accurate enough, and the angle after placing is not uniform. It is very different from similar products made in Japan." But the price of this robot is very attractive, only about half of the imported products.
Just as there are problems with domestic machine tools, there are still technical gaps between domestic robots and those mature robot manufacturers internationally such as ABB, Fanuc, and KUKA. Its main problem is the lack of research and development capabilities of key components. Major parts of the robot, such as motors and controllers, have to be purchased. Another reason is that domestic robots have poor accuracy.
According to data statistics, the mean time between failures (MTBF) calculation is that the domestic robotic products average 8,000 hours, while foreign similar products can reach tens of thousands of hours. Reliable stability has become the main reason for companies to choose "foreigners," but the high prices and high maintenance costs have deterred many companies.
It is precisely because foreign robot manufacturing companies pay too much attention to R&D and emphasizing functions, rather than paying attention to costly and usage costs, providing opportunities for domestic robots that are independently developed.
At present, many domestic scientific research institutes have professional R&D robotics projects, such as Shanghai Jiaotong University, Shandong University, and HIT, and if the machine tool company is married to these scientific research institutions, both parties will exert their respective advantages and transform the mature technologies of the scientific research institutions into products. Regardless of who is the best of both worlds.
Relying on the R&D model of “R&D core technology + mature grafting technologyâ€, domestic robot manufacturers continue to develop new products and pull down the use cost of robots, which has formed the cost advantage of mid-market competition. A person in charge of corporate technology told: "Unless the speed of innovation exceeds the speed at which I study, the odds of domestic robots will be great."
Chromium carbide thermal spray powder is a type of coating material used in thermal spray processes. It is composed of chromium and carbon, with the chemical formula Cr3C2.
This powder is commonly used in applications where high wear resistance and hardness are required. It is often applied as a protective coating on surfaces that are subjected to abrasive or erosive environments, such as industrial equipment, cutting tools, and engine components.
The thermal spray process involves heating the powder to its melting point and then propelling it onto the surface to be coated using a high-velocity gas or plasma stream. Upon impact, the molten particles solidify and bond with the substrate, forming a dense and durable coating.
The chromium carbide coating provides excellent resistance against wear, corrosion, and oxidation. It also exhibits good adhesion to various substrates, including metals, ceramics, and composites. Additionally, it has a low coefficient of friction, making it suitable for applications where reduced friction and improved sliding properties are desired.
Overall, chromium carbide thermal spray powder is a versatile and effective coating material that offers superior protection and performance in demanding industrial applications.
HVOF Powder,Chromium Carbide Powder,Chromium Carbide Coating,Chromium Carbide Thermal Spray Powder