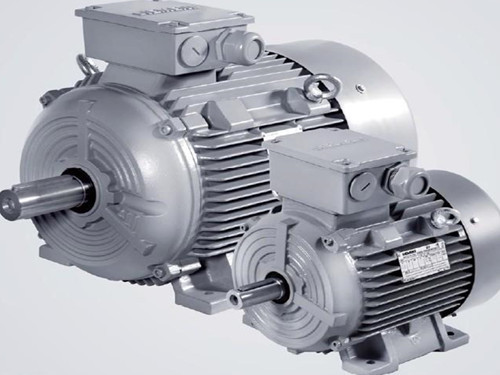
In China's industrial energy consumption ratio, motor power consumption accounts for 60%-70% of industrial energy consumption, while developed countries only account for about 45% of industrial energy consumption. At the same time, China's energy efficiency is low. Among them, the efficiency of motor systems is about 20% to 30% lower than in developed countries. Therefore, the energy conservation of electric motors has become the most critical project in industrial energy conservation. In the ten key energy-saving projects designated by China, the energy saving of motor systems is realized. Engineering is one of them.
Users lack energy-saving awareness and the market is not applauding
The high-efficiency motor refers to a universal standard motor with high efficiency motor. High-efficiency motors use new motor designs, new processes, and new materials to improve output efficiency by reducing the loss of electromagnetic, thermal, and mechanical energy. Compared with standard motors, the energy-saving effect of using high-efficiency motors is very obvious, and the efficiency can generally be increased by 4% on average.
Regrettably, although high-efficiency motors have been on the market for many years, user demand has not been very strong. At present, the market share of high-efficiency motors in China is very low, less than 10%.
Prior to the issuance of the "Circular on Printing and Energy-Efficient Products for Huimin Project High-Efficiency Motors," the issuance of high-efficiency motors has become an indisputable fact. What caused such an embarrassing situation? According to industry analysts, “domestic companies generally lack awareness of energy conservation, seldom consider hidden costs when making decisions, pay attention only to prices when purchasing equipment, and do not consider the cost of products consumed during the life cycle. In fact, the cost of a high-efficiency motor is only It is 1% of the cost of energy consumed in its life cycle."
In general, motor sales are for three types of customers: end users, agents, and equipment suppliers. The proportion of its product usage is respectively: 5% for end users, 15% for agents, and 80% for downstream machinery and equipment suppliers. It can be seen that whether the motor products can be accepted by the market and the attitude of the supporting equipment suppliers is the most critical.
So why didn't manufacturers consider high-efficiency motors when they were originally designed? The answer given by the business is simple: First, the user does not propose efficient requirements; second, the high cost of high-efficiency motors also determines its high price. As the mandatory standards and financial support policies put forward by the State on the issue of adopting high-efficiency motors have not been implemented, the high procurement costs naturally affect the end-users' purchasing enthusiasm. Equipment manufacturers, considering market demand, naturally do not choose high-efficiency motors during the initial design process.
According to a survey conducted by the International Copper Association (Beijing), the current domestic production of high-efficiency motor manufacturers only accounts for 12% of companies above designated size. Of the potential manufacturers of high-efficiency motors, 28% said that they would produce high-efficiency motors in 1 to 2 years, 41% said they would produce in 3 to 5 years, and 28% had no clear production of high-efficiency motors. plan.
Large promotion of energy-saving space is imperative
As the core component of the production line, the motor plays a crucial role in the production process. According to expert analysis, during the entire life cycle of the motor, its purchase price accounts for 2% of the total cost of the motor, maintenance costs account for 0.7% of its total cost, and energy consumption costs account for 97.3%. Therefore, using high-efficiency motors can not only increase productivity and reduce motor life cycle costs, but also reduce energy consumption and CO2 emissions. “The efficiency of our country's electrical generating units is 75%, which is 10% lower than that of foreign countries. The operating efficiency of the system is 30% to 40%, which is 20%~30% lower than the international advanced level. Therefore, in China, the electrical machinery has great potential for energy saving. Motor energy conservation is imperative, said Han Xiaoping, president of China Energy Network Information.
Relevant data shows that the average annual running time of the motor in China's industrial sector is about 3,000 hours, but in the petroleum, chemical, papermaking, metallurgy and electric power industries, the motor often needs to run for 24 hours, and the annual running time exceeds 6,000 hours. If these high-efficiency motors are used in these long-term and high-load applications, the energy saving effect will be very significant.
At present, there are mainly three ways to save energy from the motor: frequency control, energy saving, high-efficiency motor energy conservation, and use of a reactive power compensator to increase motor power factor. Among them, the average frequency conversion speed can save energy by more than 30%, the energy-saving effect is remarkable, and at the same time it has a wide range of application, and it has become one of the main ways for motor energy-saving.
Policy boosts the application process
According to industry analysts, the "Notice" has two main points: First, the more energy-efficient subsidies, the second is that the subsidy subject is a high-efficiency motor manufacturer. The "Notice" made it clear that the production enterprises are the main body for the promotion of high-efficiency motors. The central government will allocate the subsidy funds to high-efficiency motor manufacturing enterprises. The production enterprises will sell them to complete sets of equipment manufacturers, such as pumps and fans, at a subsidized price.
The timetable for the implementation of highly efficient and energy-saving motors has been determined. It is imperative to replace traditional motors. As early as 2006, the National Standardization Management Committee issued the mandatory standard "Limited value of energy efficiency and evaluation of energy conservation for small and medium-sized three-phase asynchronous motors." The document stipulates that the sales of level 3 energy-efficiency motors will be banned after July 1, 2011, which means 2012. After years, highly efficient and energy-saving motors will fully replace traditional high-energy motors.
At present, the transition period is coming to an end, and it is expected that the promotion of highly efficient and energy-saving motors will increase.
Some analysts believe that the market size of small and medium-sized motors will continue to grow and is expected to reach more than 60 billion yuan by 2012. However, the proportion of high-efficiency energy-saving motors is still relatively low. In 2008, the proportion of highly efficient energy-saving small and medium-sized motors that reached Grade 2 or above was only 8%. %.
With the implementation of the financial subsidy policy and the lower base figure, it is expected that the energy-efficient motors will show explosive growth, and the market will focus on the leading companies that have taken the lead in layout, leading companies will benefit from industry growth.
High-efficiency motors mainly save energy through frequency conversion. Therefore, some analysts believe that the future market of high-voltage inverters is the most optimistic.
At present, high-voltage inverters have become the standard configuration for many new construction projects. If the national cement design standard stipulates that since May 1, 2008, the high temperature fan of the new cement rotary cellar production line must adopt high-voltage frequency conversion; many new thermal power generating units have adopted the frequency conversion speed regulation of the condensate pump as the standard for the bidding of the auxiliary machine. Projects, so the market space in China is still huge.
3 Ton Multi-directional Forklift
Zowell RSEW130 Multi-Directional Forklift is a material handling equipment specialized for long and bulky material handling and stacking. Its unique design covers the advantages of common forklifts and stackers as well as VNA trucks. With three omni-directional wheels, it can drive in multiple directions such as parallel moving and oblique moving, so as able to maneuver smaller aisles and maximize your warehouse storage safely.
As a company with experience on narrow aisle electric forklifts for more than 15 years, Zowell always focuses on professional warehouse solutions and customer experience. In terms of power supply, RSEW adopts electric power featured with low noise and no emission, and can be equipped with lithium battery with convenient maintenance and longer service life. In terms of control, the load wheels are equipped with the five-stage steering deceleration and small control current, which enables the steering angle more precise and controllable, effectively extend the service life of the steering motor. From the aspect of security, Zowell multi-directional forklift is equipped with steering wheels display system and barking system to maximize safety.
hubtex multidirectional forklift,multi directional reach forklift,multi directional forklift price,multi directional forklift brands
Suzhou Pioneer Material Handling Equipment & Technology Co., Ltd , https://www.xianfengforklifts.com