Introduction: Regardless of whether it is a cement vertical mill or a slag vertical mill, whether it is a vertical mill with the same force or a vertical mill produced by other units, the working principle of the vertical mill is basically the same. Even if there is a difference, it is just different parameters. The operation, use, and maintenance of the equipment all have similarities. The following are some of the measures for improving production of slag mills (for reference only).
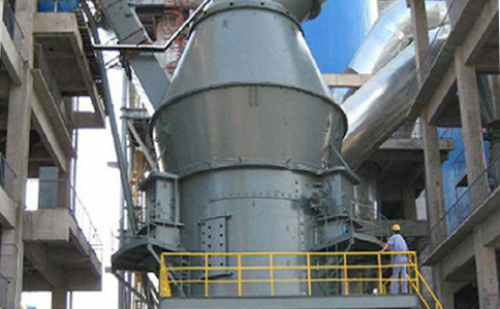
(1) cement vertical grinding operation skills
Suitable material thickness. The vertical mill adopts the material bed pulverization principle, and the stable material layer is the prerequisite for the continuous stable operation of the vertical mill. The material layer is too thick, the grinding efficiency is low, and the current is high. The material layer is too thin, and it is easy to cause mechanical vibration. Therefore, according to the wear condition of the vertical roller skin and the disc lining plate, the height of the material block should be timely adjusted to control a reasonable material layer.
Material comprehensive moisture should be controlled at 2% to 5%. The material is too dry and fine and has good fluidity and it is difficult to form a stable material layer. At this point should be appropriate to increase the height of the block, reduce the grinding pressure or spray water (2% -3%) to reduce the material flow, in order to facilitate the stability of the material layer; the material is too wet, will affect the ingredients station, belt scales, etc. The equipment operates stably, thus affecting the hourly output. It can be seen that controlling a stable and reasonable material layer, maintaining reasonable temperature and humidity, and maintaining a slightly high pressure difference is a good way to achieve vertical mill production and energy conservation.
Suitable for grinding pressure. The cement vertical mill uses a hydraulic system to apply grinding pressure to the grinding roller to comminute the material on the grinding bed. As the pressure increases, the output of the mill increases, and the output power of the mill motor increases accordingly. According to the nature of the actual milled material, particle size, production, wind speed, etc. to find out the corresponding relationship between grinding pressure and output. Determining a suitable grinding pressure is an important parameter to increase the production of the table. It is important to practice the proper grinding pressure for the company's slag mill.
Suitable for reasonable wind speed. Vertical mills mainly depend on the airflow for animal circulation and transportation. Since the nozzle ring area S is determined to be constant, it can be seen that the air volume Q=wind speed V×area S. The air volume must first meet the requirements of conveying materials. The lack of air volume will cause the qualified raw materials to not be brought out in time, which will increase the thickness of the material layer, increase the amount of slag discharge, increase the load of the mill, and reduce the output. The air volume is too large to increase wear in the mill. The effect of cyclone dust collection deteriorates, and at the same time it brings unstable factors to the operation of the mill. Therefore, the control of reasonable wind speed and air volume is very important for maintaining the stability of the material layer and achieving long-term, stable, and efficient operation of the mill.
(2) Factors affecting cement vertical mill machinery
Hydraulic system. The hydraulic system is the main component for applying pressure and maintaining pressure to the vertical grinding roller. In general, the grinding pressure is proportional to the output. The higher the grinding pressure is, the higher the output is. However, once the limit is exceeded, the load of the mill will be increased or even the useless work will be increased. It will also cause vibration and affect the stable operation of the mill. Therefore, as far as possible, the reasonable combination of grinding pressure and layer thickness should be ensured in order to achieve the best grinding effect. Hydraulic system pressure leaks, it is difficult to maintain pressure. Therefore, in the event of hydraulic cylinder damage, oil leakage or nitrogen balloon pressure imbalance, etc., it should be repaired in time.
Cement vertical mill spout ring. The main function of the spout ring is to change the direction of the wind by the guide vanes, and to ensure that the gas flow turns upwards to take away the material. If the nozzle ring or part is worn, the airflow will be disordered, and a stable spiral upward airflow field will not be formed. The wind speed will also decrease, so that the material can not be taken away in time and return to the grinding wheel or fall into the scraping chamber at the bottom of the nozzle ring to increase the circulation volume. , And then affect the mill output and operating stability.
Cement vertical mill lining. Due to the centrifugal force of the disc, large pieces of material are easily concentrated in the edge area of ​​the disc. Therefore, the wear of the outer surface of the grinding roller and the disc plate is often larger than that of the inner side. After the grooves are formed by wear, a large amount of material cannot be obtained well in this area. Grinding and overflowing the retainer ring enters the discharge ring area, resulting in an increase in the amount of slag discharge and a decrease in the yield.
Cement vertical mill retaining ring. The function of the retaining ring is to allow the material to be fully ground on the disc. When the material properties and the mill operating parameters are stable, the height of the retaining ring basically determines the maximum thickness of the material layer. After the block ring is worn, materials that are not fully ground will be thrown out of the disc under the effect of centrifugal force, resulting in increased slag discharge and increase in the amount of return material. The vibration of the mill will also become large, and only low-production operation can be maintained and easy. Downtime occurred.
Cement Vertical Mill Separator. In the long-term operation, the guide vanes of the separators will have a large area of ​​varying degrees of wear, which will greatly reduce the effectiveness of their guiding air flow. The cyclone of the belt material will be disturbed, and the classification efficiency will not be reduced at a constant speed through the guide vanes into the internal cage rotor. .
(3) Factors affecting the vertical mill process
The granularity of the material. The vertical mill has a certain range of requirements for the grain size of the milled raw materials, generally less than 80mm and 30mm each, and the maximum grain size is preferably not more than 5%, otherwise it will affect the vertical mill output. If the block material is too large, the larger the circulation volume, the higher the differential pressure and increase the vibration of the equipment. If the particle size is too large or too small, the gradation balance of the material layer will be destroyed, which will affect the stable operation of the equipment.
The grindability of the material. Grindability refers to how difficult it is for the material to grind to a certain degree of fineness. The vertical mill grinds the number of grinds that have poor grindability and increases the number of external circulations. In particular, the differential pressure becomes large, the load on the mill and separator becomes large, and the raw material fineness becomes coarse. Sacrificing the yield is to ensure the fineness of the raw meal by reducing the amount of feed. At the same time, the poor wearability of the material on the grinding roller, grinding disc liner wear intensified, and its maintenance also increased. Therefore, according to the change of the ratio of the materials or batches of the incoming mills, regular wearability should be tested, and with the laboratory's reasonable deployment, the process and equipment parameters should be optimized to ensure stable and high-yield operation of vertical mills.
System air leakage. Cement expansion system expansion joints, connecting flanges, three inlet valves, spout rings, slagging outlets, etc. are prone to air leakage, which reduces the wind speed in the mill, and the finished materials cannot be taken away in time by the air flow, or the pipeline is caused The accumulation of elbows, clogging, and reduced ventilation area will affect the mill output. Therefore, on-duty operators are required to conduct inspections at any time and deal with them in a timely manner.
"Gravity Die Casting. A permanent mould casting process, where the molten metal is poured from a vessle of ladle into the mould, and cavity fills with no force other than gravity, in a similar manner to the production of sand castings, although filling cn be controlled by tilting the die."
Gravity Die Casting
Sometimes referred to as Permanent Mould, GDC is a repeatable casting process used for non-ferrous alloy parts, typically aluminium, Zinc and Copper Base alloys.
The process differs from HPDC in that Gravity- rather than high pressure- is used to fill the mould with the liquid alloy.
GDC is suited to medium to high volumes products and typically parts are of a heavier sections than HPDC, but thinner sections than sand casting.
There are three key stages in the process.
- The heated mould [Die or Tool] is coated with a die release agent. The release agent spray also has a secondary function in that it aids cooling of the mould face after the previous part has been removed from the die.
- Molten metal is poured into channels in the tool to allow the material to fill all the extremities of the mould cavity. The metal is either hand poured using steel ladles or dosed using mechanical methods. Typically, there is a mould [down sprue" that allows the alloy to enter the mould cavity from the lower part of the die, reducing the formation of turbulence and subsequent porosity and inclusions in the finished part.
- Once the part has cooled sufficiently, the die is opened, either manually or utilising mechanical methods.
Advantages
- Good dimensional accuracy
- Smoother cast surface finish than sand casting
- Improved mechanical properties compared to sand casting
- Thinner walls can be cast compared to sand casting
- Reverse draft internal pockets and forms can be cast in using preformed sand core inserts
- Steel pins and inserts can be cast in to the part
- Faster production times compared to other processes.
- Once the tolling is proven, the product quality is very repeatable.
- Outsourced Tooling setup costs can be lower than sand casting.
Gravity Casting Parts,Aluminum Alloy Gravity Casting Parts,Aluminum Gravity Die Casting Parts,Gravity Casting Aluminum Parts
HSI INDUSTRIEL LTD , https://www.hsiindustriel.com